蠟模成形不良-缺料(未充滿)

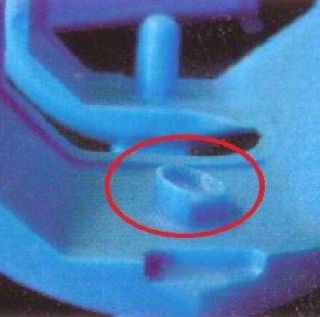
產生原因 | 防止措施 | |
---|---|---|
製模工藝 | 1. 蠟溫偏低 2. 射蠟壓力不足 3. 模具溫度低 |
1. 適當提高蠟溫 2. 適當提高射蠟壓力 3. 適當升高冰水溫度,製作大尺寸薄壁蠟模,需適當預熱模具 |
設備 | 1. 射嘴內徑小 2. 射嘴中有殘留冷蠟塊 |
1. 加大射蠟嘴內徑尺寸 2-1. 射蠟前清除射嘴中殘留冷蠟塊 2-2. 適當提高射嘴溫度 2-3. 改進射嘴結構,避免射嘴產生冷蠟塊 |
模具 | 1. 蠟模型腔排氣不順 2. 注蠟口位置不當或太小 |
1. 增加排氣孔或使用排氣塞 2. 必要時另選位置重開注蠟口或加大直徑 |
模料 | 蠟膏流動性差 | 必要時更換模料 |
冷接-冷隔
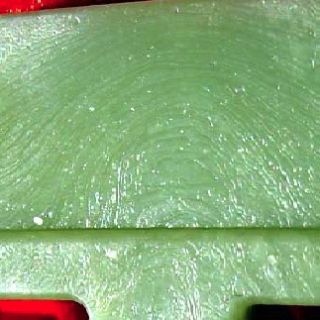
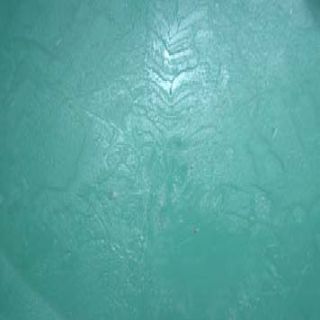
產生原因 | 防止措施 | |
---|---|---|
製模工藝 | 1. 蠟溫偏低 2. 射蠟壓力不足 3. 模具溫度低 |
1. 適當提高蠟溫 2. 適當提高射蠟壓力 3. 適當升高冰水溫度,製作大尺寸薄壁蠟模,需適當預熱模具 |
設備 | 1. 射嘴內徑小 2. 射嘴中有殘留冷蠟塊 3. 射蠟流速慢 |
1. 加大射蠟嘴內徑尺寸 2-1. 射蠟前清除射嘴中殘留冷蠟塊 2-2. 適當提高射嘴溫度 2-3. 改進射嘴結構,避免射嘴產生冷蠟塊 3. 加快射蠟流速,必要時更換射蠟機 |
模具 | 1. 射蠟口位置不當或太小 2. 模具型腔表面不光滑 |
1. 加大射蠟口直徑,同時確認射蠟流道合理性 2. 整修模具,模具進行研磨、拋光 |
模料 | 1. 蠟膏流動性差 2. 蠟膏溫度不均勻 |
1. 必要時更換模料 2. 仔細控制射蠟缸內蠟膏溫度,確保蠟膏溫度均勻 |
流紋-流線
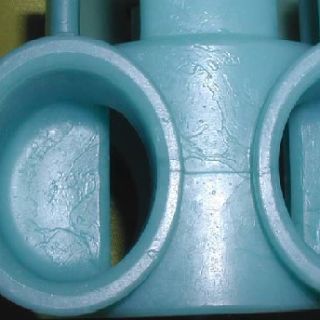
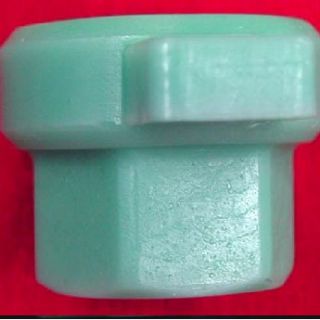
產生原因 | 防止措施 | |
---|---|---|
製模工藝 | 1. 蠟溫偏高 2. 模具溫度偏低 |
1. 適當降低蠟溫 2. 適當提高模具溫度 |
設備 | 1. 射嘴內徑大 2. 射蠟速度過快,蠟進入模具後產生擾流或噴濺 |
1. 縮小射蠟嘴內徑尺寸 2. 降低射蠟速度。避免產生擾流或噴濺 |
模具 | 1. 射蠟口位置不當或太大 | 1. 必要時重開射蠟口或縮小直徑 |
表面粗糙
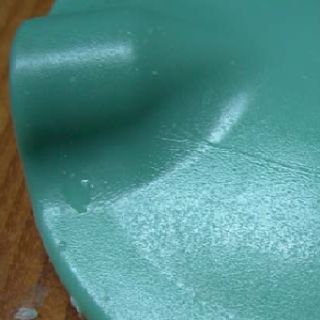
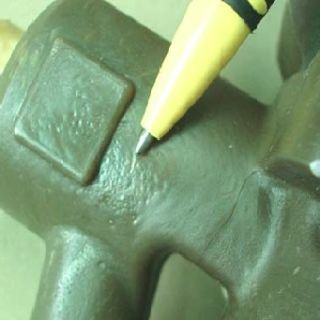
產生原因 | 防止措施 | |
---|---|---|
製模工藝 | 1. 蠟溫偏低 2. 射蠟壓力不足 3. 模具溫度低 |
1. 適當升高蠟溫 2. 適當提高射蠟壓力 3. 適當升高冰水溫度,製作大尺寸薄壁蠟模,需適當預熱模具 |
設備 | 1. 射蠟機額定射蠟壓力太小 | 1. 選用合適的射蠟機 |
模具 | 1. 模具型腔表面不光滑 | 1. 整修模具,模具進行研磨、拋光 |
模料 | 1. 蠟膏溫度不均勻 2. 蠟膏成份不均勻 3. 蠟內含過多殼模或灰份 |
1. 仔細控制射蠟缸內蠟膏溫度,確保蠟膏溫度均勻 2. 脫蠟後適當加入新蠟料,必要時更換新蠟 3. 脫蠟後給於足夠的靜置時間,使殼模或灰份沉澱 |
飛邊-毛刺
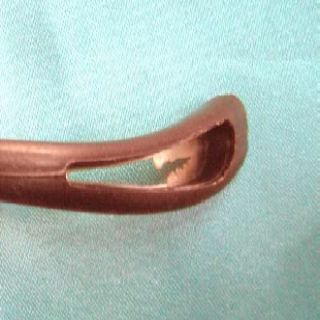
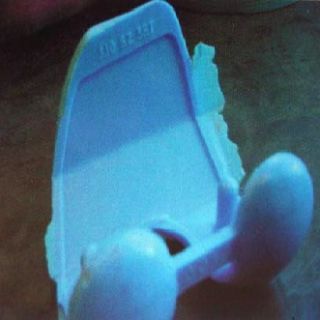
產生原因 | 防止措施 | |
---|---|---|
製模工藝 | 1. 蠟溫偏高 2. 射蠟壓力太大 3. 壓模壓力太小 |
1. 適當降低蠟溫 2. 適當降低射蠟壓力 3. 適當提高壓模壓力 |
設備 | 1. 額定壓模壓力太小 | 1. 選用合適壓模噸數的射蠟機 |
模具 | 1. 模具型腔磨損或損壞 2. 合模不嚴 3. 模具抽芯、滑塊等配件過鬆 |
1. 整修模具,確認分模面邊緣有無損傷 2. 仔細清理模具分模面,便免殘留蠟屑或其他雜物 3. 反修模具 |
其他 | 1. 模具安裝偏離壓模油缸中心,導致模具受力不均勻 | 1. 重新安裝模具,確保模具中心對準壓模油缸中心 |
表面縮陷或蠟模變型
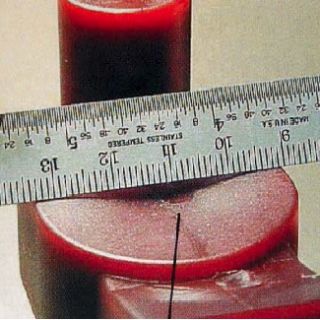
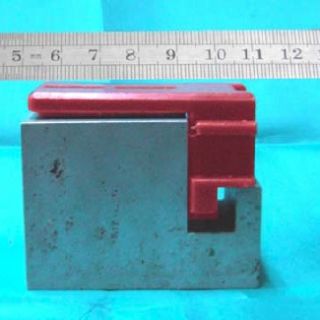
產生原因 | 防止措施 | |
---|---|---|
製模工藝 | 1. 蠟溫偏高 2. 射蠟、保壓壓力太低 3. 保壓時間不足、蠟冷卻時間不足 4. 模具溫度偏高 |
1. 適當降低蠟溫 2. 適當提高射蠟、保壓壓力 3. 適當提高保壓、蠟冷卻時間 4. 降低模具冰水溫度 |
設備 | 1. 射蠟機蠟處理能力不足 | 1. 選用能穩定保持較低射蠟溫度的射蠟機 |
模具 | 1. 模具注蠟口小而長 2. 注蠟口位置不當 3. 蠟模頂出機構設計不當 4. 帶盲孔的蠟模,抽出抽芯時產生負壓造成變型 |
1. 加大注蠟口截面積,縮短蠟澆口長度,使保壓時蠟料能補入蠟模 2. 將注蠟口位置改在靠近易產生變型的厚大位置 3. 增加頂出點使蠟模受力均勻 4. 修改抽心拔模角度或增加氣道 |
模料 | 1. 模料選擇不當 | 1. 選用收縮率小的蠟料,必要時改用填充蠟 |
其他 | 1. 脫模劑選用不當或噴塗不均勻 2. 起模過快或方法不當 3. 蠟模存放方式不當 4. 環境溫度過高 |
1. 選用合適脫模劑,定期且均勻噴塗,確保脫模順利 2. 對員工進行脫模培訓,或改用自動模具 3. 蠟模取出後可放在適當的校正製具上,直到蠟模完全冷卻後再移出 4. 嚴格控制製模車間、蠟模存放工作場地溫度 |
氣泡
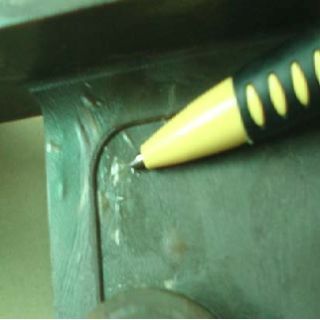
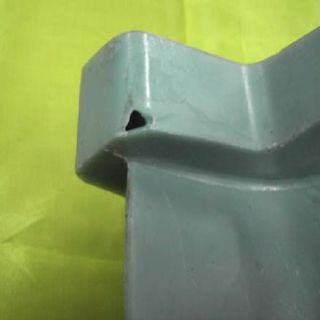
產生原因 | 防止措施 | |
---|---|---|
製模工藝 | 1. 蠟溫偏高 2. 射蠟速度過快,導致氣泡捲入 |
1. 適當降低蠟溫 2. 降低射蠟速度 |
設備 | 1. 蠟處理系統無法順利將蠟內空氣排出 2. 管路輸送過程中捲入空氣 3. 射蠟機製膏過程中捲入空氣 |
1. 選用合適的蠟處理系統 2. 變更管路輸送方式,降低送蠟速度或蠟進入蠟桶高度 3. 更換射蠟機相對應軸封,或更換成製膏過程不會捲入空氣的射蠟機 |
模具 | 1. 排氣設計不良 2. 注蠟口小或位置不當 |
1. 增加模具排氣 2. 修改注蠟口尺寸或位置 |
模料 | 1. 使用陶瓷蠟料,倒蠟入蠟桶或攪拌產生的氣泡 | 1. 蠟桶增加負壓功能,加強蠟料排氣 |